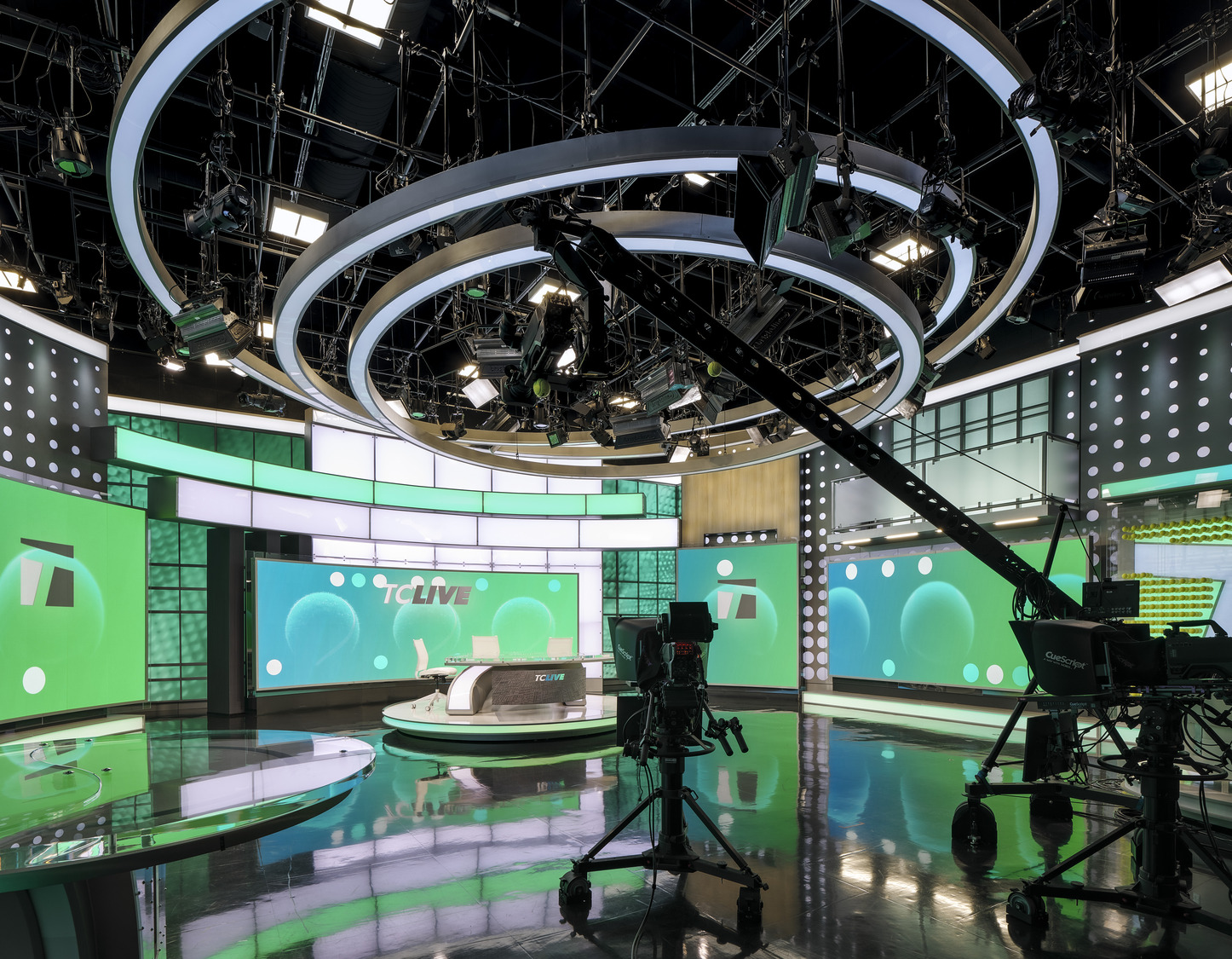
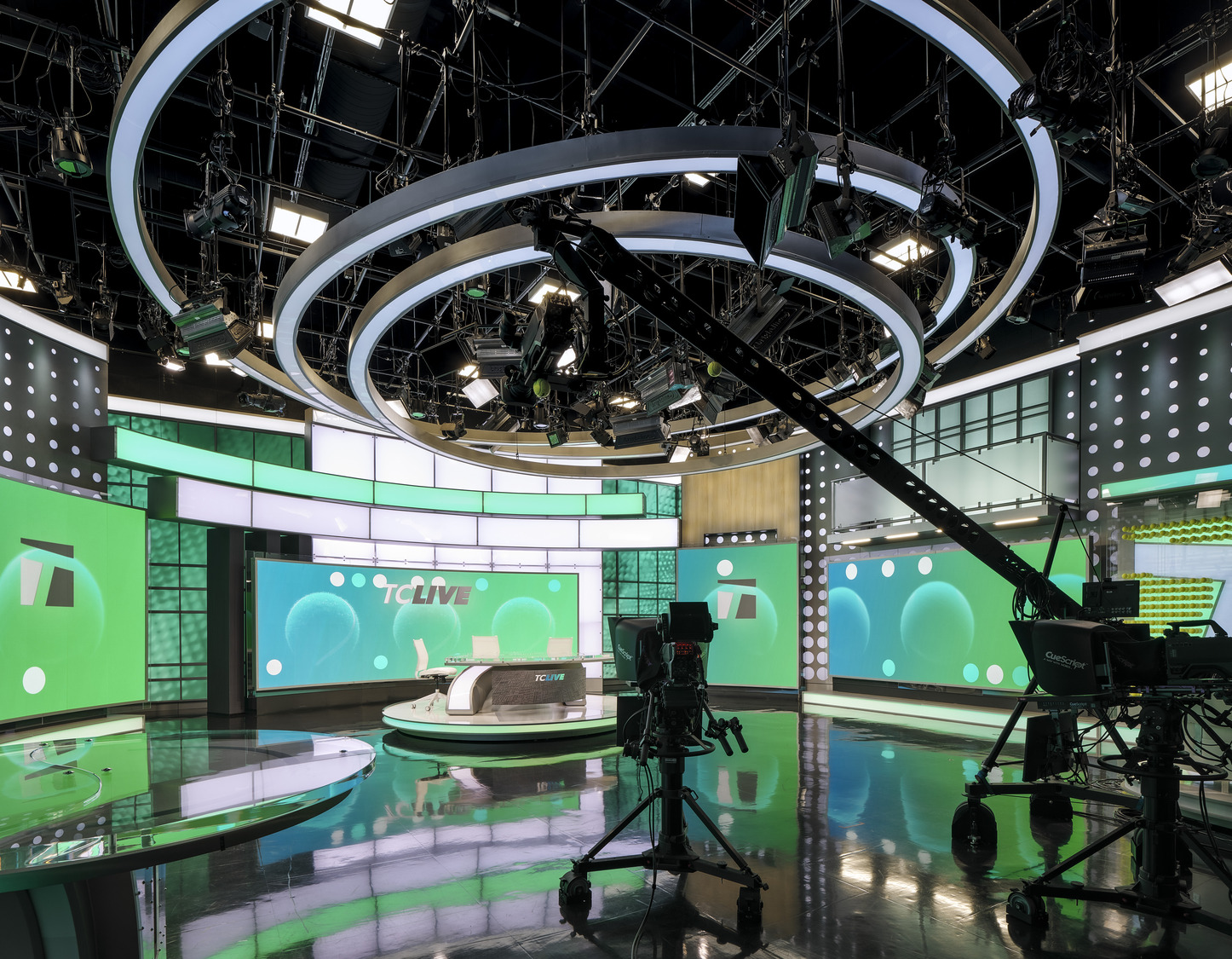
16 May 2022
By: Joe Glynn
Virtual construction continues to become an even more critical component on jobsites, as technological capabilities expand. Over the last few years, Clune’s in-house Virtual Construction department has been focused on providing visualization options in a world of social distancing and limited travel. While these communication tools are still a major focus for the team, a new focus has been added to their tool box – quality control.
Checking our Work
Virtual construction and Building Information Modeling (BIM), often come into play during the pre-construction phase of a project. They can also be equally useful when the project is wrapping up. On some of our larger projects, the team will create an initial model of the space that is approved by the client during the pre-construction phase. This model then serves as the road map for the entire build-out.
Once the project is nearly complete, a virtual construction team member will re-scan the job site. The laser scanners utilized are hand held, easily transported, and the scanning process takes only a matter of minutes. When the scan is complete, the team will overlay the point data over the original BIM model and perform a visual and computational check to ensure that all the elements of the build were installed properly.
For example, if ceiling ductwork is a few inches lower than planned there could be a major issue that will need to be addressed. If a power distribution unit (PDU) that will be installed towards the end of a project needs a very specific amount of clearance, a few inch discrepancy could cause major financial and schedule implications. In either situation, knowing that there is a discrepancy allows the team to make a change before it becomes costly.
Benefits to Owners
The above example is a great illustration of where that extra layer of checks and balances for our subcontractor partners can provide a huge benefit. Depending on the critical nature of a build, these types of checks could occur multiple times throughout a project.
For data center construction, this quality check would occur, at a minimum, right before commissioning. The information would then be utilized to ensure the planned specifications were built exactly correct, and if there are small shifts (that don’t cause any issues) they are edited in the BIM model. That model is eventually turned over to the owner as an as-built file for space maintenance and/or future renovations.
Additional Tools
By focusing on understanding our client’s priorities, our team is able to determine which tools are needed to ensure a successful project. Having a “purpose-built tech box” to pull from is a priority of our VC department. Clune’s tech box includes comprehensive 3D laser scanning, BIM, Augmented Reality (AR), Virtual Reality (VR), and soon drone imaging services.
The team is consistently altering our processes and technology, and are merging them with new technologies, to enable clients to stay connected, informed and to easily communicate about a construction projects.
Learn more about Clune’s Virtual Construction team and capabilities here.