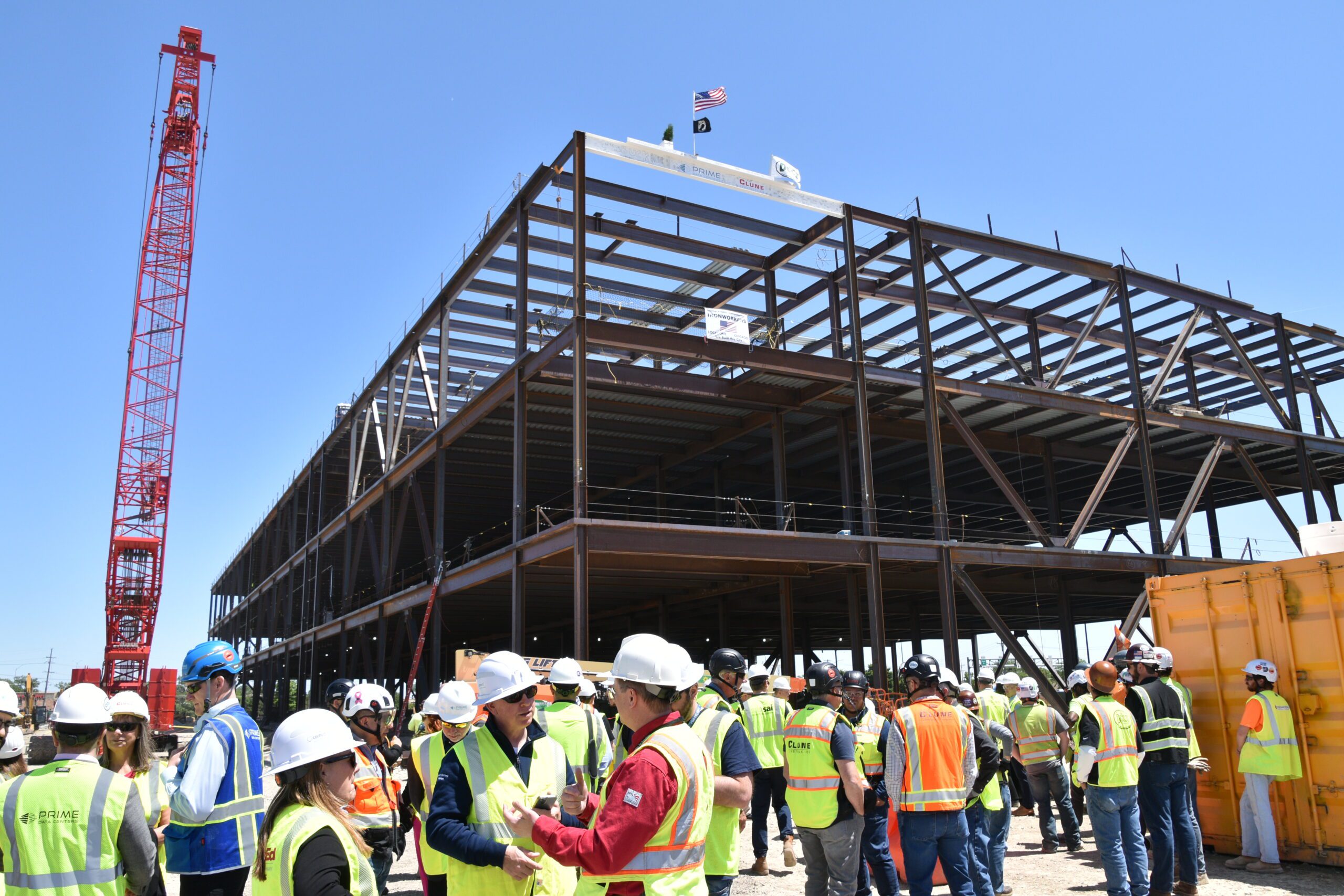
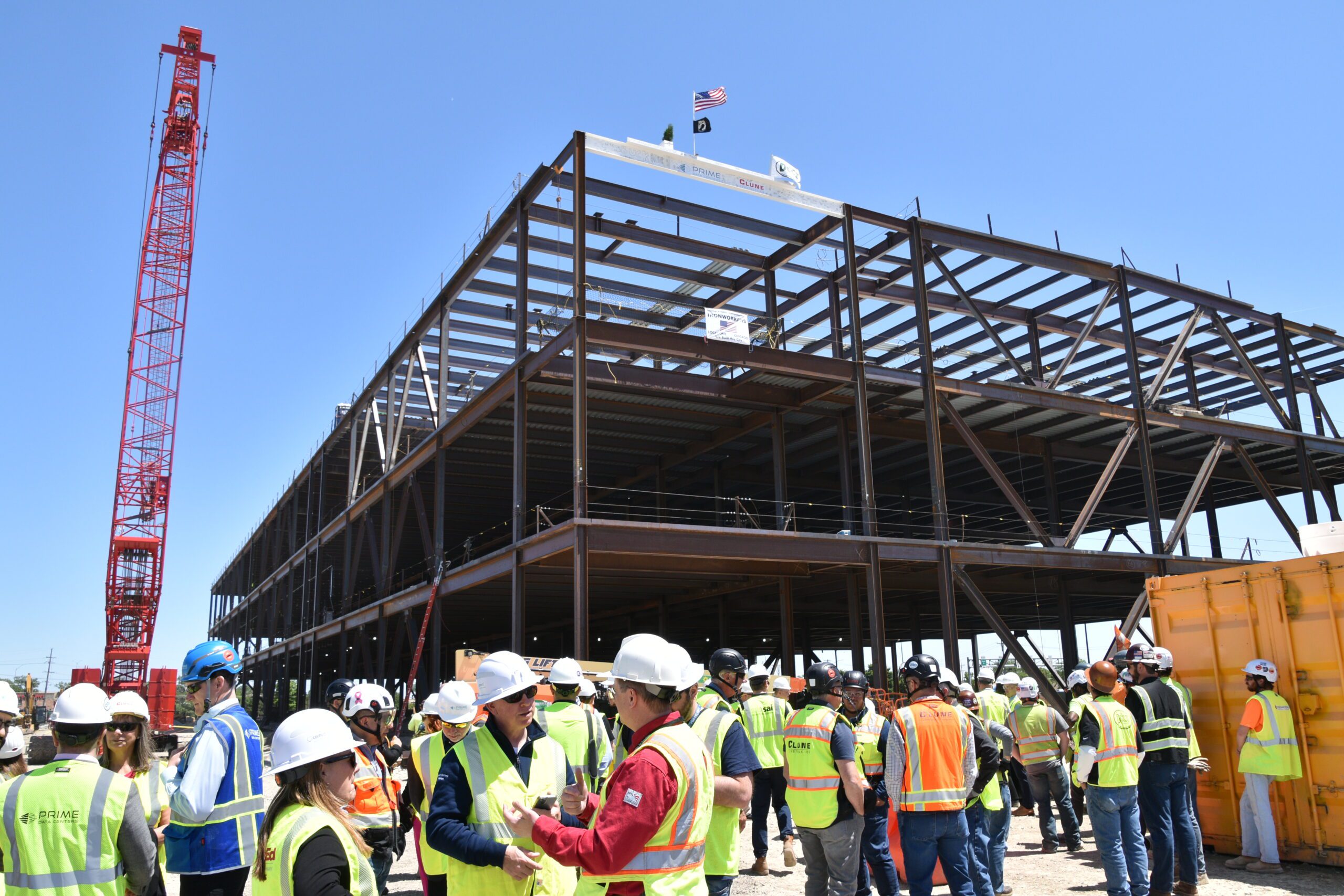
25 February 2021
By: Jack Murphy, Senior Project Manager
While COVID-19 has severely impacted most sectors of the construction industry, data center construction continues to climb at unprecedented rates. As the pandemic continues, the exponential increase in data usage is adding increased demand for storage capacity. Data center providers are faced with the challenge of how to manage this growing demand, while also expanding capacity. Providers are considering large scale capital investments to either finance a new site, or to increase the density of an existing location.
Construction trends historically follow the processes that prioritize speed and efficiency. This has shortened the average data center build and deployment time. Contractors and their partners, including owners and designers, are finding new ways to be innovative to keep up with the rapid speed of implementation. The result has been a tidal wave of pre-fabrication and modular construction in the data center market.
Modular construction in data centers is not a new concept. This trend has been growing in popularity over the last few years. Modular electrical rooms are portable solutions for deploying data processing capacity, delivering large amounts of power within a small footprint and a tight timescale. Modular power units are built and tested in a controlled environment to comply with the project specifications. The portable power solutions are then shipped fully built and tested to the site, ready for immediate installation. The result is a dramatic reduction in onsite labor hours surrounding MEP activities. The flexibility of modular power construction can streamline data center projects from planning through commissioning. This has solidified modular design as a key component of future data center construction.
Pre-Fabricated Solutions for Quick Deployment Timelines
Expertly qualified contractors will offer pre-fabricated MEP solutions in order to meet the timelines of today’s data centers. Power distribution and cooling solution providers have recognized the opportunity to improve deployment speed by offering the newest solution in the race for sellable white space – pre-fabricated power modules.
Pre-fabricated modules are engineered, assembled data center physical infrastructure systems. They are delivered as standardized “plug-in” modules to a data center site.
Examples of physical infrastructure systems that provide these opportunities are:
Enclosed Electrical Rooms vs. Open-Framed Power Skids
The two most common pre-fabricated power modules are modular enclosed electrical rooms and open-framed power skids. From the exterior, enclosed power modules resemble a shipping container. They are weather tight and can deliver many megawatts of power to support a facility’s IT load.
Open-framed power skids have the same guts as the enclosed power module but are not enclosed. These modules are typically skidded on steel dunnage. If properly planned, both solutions offer similar power deployment benefits. However they are utilized in different scenarios.
Enclosed Electrical Rooms
An enclosed electrical room can be installed on the exterior of the facility. This is an effective method for deploying power infrastructure outside of an existing data center facility where square footage is limited. Enclosed power modules eliminate using potential white space for power distribution. They provide a more time-sensitive and cost-effective solution to acquiring or constructing a new brick and mortar facility to satisfy expansion.
Open Framed Power Skids
Open-framed power skids, are effective for quick deployment, but don’t offer the same protections as enclosed rooms. The skids are ideal for data centers that have available indoor space. They can be produced in anticipation of deployment and rigged through a facility’s exterior structural wall to provide power to a space that requires densification. The downside to this approach, is it takes away square footage that could be used as sellable space. However, if a provider pre-plans their structure to accept skidded power rooms, they can effectively and quickly deploy power to their facility.
Pre-Fabricated Data Centers for a Safer Jobsite
The utilization of pre-fabricated modular power results in a reduction of man hours required for hoisting, setting and assembling, which contributes to a safer jobsite. Material handling and settling of the electrical room equipment can present safety challenges on a traditional data center project. These activities are high risk because the movement of equipment or materials using mechanical means (such as pallet jacks, casters, powered industrial equipment), if utilized improperly, can cause injury to workers or damage to equipment that can result in a schedule delay.
Another risk to worker safety on a typical data center project is electrical rooms, which are are typically located adjacent to the white space. This is done to minimize conduit and cabling from output boards to the power distribution on the data hall floor. The central location of electrical rooms within a data center can cause congestion and increase the risk of injury and incident. Controlled access zones are employed while the equipment is being rigged to control the flow of traffic, restrict access to the area, and reduce congestion. However, rigging multiple electrical rooms can take weeks to complete. Utilizing controlled access zones for the rigging area can affect the overall flow of the jobsite, causing logistical nightmares for the affected trades.
Pre-fabricated electrical rooms reduce on-site man hours to ready a power block. This allows a seamless sequencing of work around the space, thereby reducing the safety risk to those on-site.
Pre-Fabricated Modular’s Impact Lead Times
The efficiencies gained through using pre-fabricated modular power skids are evident. Since they are delivered to the site pre-assembled and partially tested, the amount of man hours during construction and commissioning decreases.
This contrasts the traditional approach where all coordination, assembly, installation, and integration take place on-site. With the appropriate time given to pre-construction and planning, the implementation of pre-fabricated power modules can impact project lead times significantly. The deployment of prefabricated power modules can be up to 40% faster.
However, the lead times of a pre-fabricated power modules are much longer than those of major equipment in a traditional deployment scenario. This is because the pre-fabricated solution adds additional steps to the procurement process. The power distribution, cooling equipment, and BMS/controls pathways must be assembled on the open frame power skid. An enclosed module also requires the installation of fire protection and VESDA systems. Proper pre-construction and planning is crucial in order to gain the many efficiencies they can offer.
The on-site integration of pre-fabricated power modules can be less complex than traditional integration. This is because each power module should arrive with the interconnect wiring complete, the equipment piped and the wire to the local BMS controller or panel within the module itself. If wired correctly by the manufacturer, power and cooling infrastructure can be integrated quickly to the base building system.
The focus of data center providers around the globe is to be quickly able to deploy power and cooling in order to sell or build white space at specific scales and specifications from customers. Pre-fabricated power modules extract assembly and man hours from the field and can drastically reduce the deployment time for data center providers.
Our Expertise
Clune’s Mission Critical team has years of experience building data center facilities with and without pre-fabricated options. During the pre-construction process, Clune works closely with the client and design team to determine their best options, focusing on the project completion date. As a trusted partner, Clune evaluates functionality and lead times of equipment and makes recommendations in the best interest of the end user. With more data storage demand than ever before, our teams understand the importance of quick construction. We also understand that a data center can hold the key to a company’s entire operation, and even a short outage can be devastating. Clune’s team has the expertise needed to construct a data center that can handle its critical day-to-day operations.
About the Author
Jack Murphy started with Clune Construction as an intern in the Mission Critical Group. Since then he has worked his way through the ranks to become a Senior Project Manager. He has the proven skills and knowledge to lead teams on major data center construction projects throughout the Midwest region. Jack has overseen construction of high profile data centers in the Chicago area and Columbus, Ohio. He earned his Bachelor of Science in Technical Systems Management from the University of Illinois, Champaign-Urbana.